Le projet LIFE Multi-AD 4 AgroSMEs a pour objectif de développer un réacteur anaérobie multiphase à haute performance en vue de son industrialisation, qui génère du biogaz riche en méthane, spécialement conçu pour le traitement des eaux usées générées dans les petites et moyennes entreprises de l’industrie alimentaire et des boissons.
Le bon fonctionnement d’un réacteur anaérobie dépend du maintien des facteurs environnementaux à proximité de la zone de confort des micro-organismes. Par exemple, les changements de température, de pH ou de concentration en matière organique des eaux usées peuvent entraîner l’arrêt de la production de biogaz. Ainsi, les paramètres clés de ce processus sont : la température, le pH, le potentiel redox, le taux de charge organique, la concentration en solides et en nutriments.
L’un des objectifs spécifiques du projet LIFE Multi-AD est de développer, d’optimiser et d’automatiser le système de contrôle afin de maximiser la stabilité du processus anaérobie et de le rendre robuste aux changements de composition des eaux usées ou des conditions de fonctionnement. Le système de contrôle ajustera automatiquement les variables de sortie contrôlables (température, pH, total des solides en suspension (TSS), demande chimique en oxygène (COD), débit des eaux usées), en utilisant des algorithmes et des fonctions logiques. Les principales fonctions du système d’automatisation sont : la surveillance du niveau, de la DCO, des MES, de la température et du pH dans les réservoirs, l’affichage des paramètres et l’alerte de l’opérateur lorsque les paramètres des limites normales de fonctionnement sont dépassés.
Le système d’automatisation a été développé sur la base d’un schéma technologique innovant, qui comprend des détails sur la façon dont les eaux usées de l’industrie des boissons sont fournies à la station d’épuration des eaux usées pour alimenter le réacteur Multi-AD et comment le biogaz résultant est traité pour permettre une capitalisation supplémentaire.
Le projet LIFE Multi-AD a terminé avec succès la phase de développement du système de contrôle avancé pour l’automatisation du contrôle des paramètres du processus. A ce stade, sur la base des résultats des actions précédentes, une unité de travail de démonstration 1 : 1 du réacteur Multi-AD à une échelle industrielle de 100 m3 a été construite pour valider ses performances.
La part de SIS dans ce projet était l’automatisation de l’ensemble du processus. Ce voyage a commencé dès la phase de conception, lorsque nous avons analysé le processus et créé la meilleure configuration pour l’armoire d’automatisation de cette application. De plus, nous avons utilisé TIA Portal V16 pour programmer la logique, en utilisant une approche « Cause-effet », interconnectant ainsi toute la station et rendant l’opération aussi sûre que possible. Les procédures de simulation et de test ont été effectuées à l’aide de l’extension PLCSim, afin de garantir que nous livrons une logique qui fonctionne comme un charme.
L’automatisation ne signifie rien si vous ne pouvez pas la contrôler et la surveiller, c’est pourquoi nous avons développé deux solutions pour cette application.
La première est une interface IHM physique, placée sur l’armoire d’automatisation, créée à l’aide du logiciel WinCC Siemens. Il s’agit d’une représentation graphique de l’ensemble de la station, qui permet à un opérateur de modifier facilement les points de consigne, d’activer et de désactiver les pompes, de surveiller les valeurs et bien plus encore.
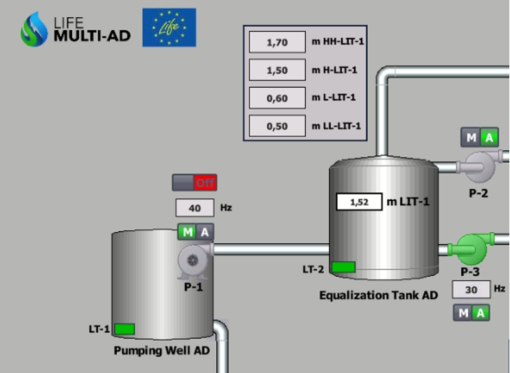
L’interface opérateur se compose de dix écrans : l’écran principal, quatre écrans de détail, l’écran de la pompe, l’écran électrique, l’écran de la minuterie et l’écran d’alarme. L’écran principal présente le schéma complet du système et permet de naviguer vers les autres écrans grâce aux boutons. Les écrans de détail ont pour but de suivre chaque zone du système avec tous les éléments et paramètres qui leur sont associés. Dans l’écran des limites sont visibles toutes les valeurs extrêmes du système sur chaque élément avec la possibilité d’ajustement par l’opérateur. La liste des messages d’alarme du système est disponible dans l’écran des alarmes.
L’unité de démonstration Multi-AD réalisée a été installée et a été testée sur le système avec la possibilité de la redessiner, pouvant ainsi optimiser son modèle et ses paramètres opérationnels. Enfin, le fait que le réacteur Multi-AD soit entièrement automatisé avec un contrôle avancé fait partie du concept d’industrie 4.0, car notre dispositif utilise un grand nombre de capteurs et met en œuvre des machines de calcul intelligentes, entre autres technologies.
Ce projet LIFE Multi-AD offre une solution technologique innovante, prête à être adoptée par les petites et moyennes entreprises de l’industrie alimentaire et des boissons.
L’interface opérateur se compose de dix écrans : l’écran principal, quatre écrans de détail, l’écran de la pompe, l’écran électrique, l’écran de la minuterie et l’écran d’alarme. L’écran principal présente le schéma complet du système et permet de naviguer vers les autres écrans grâce aux boutons. Les écrans de détail ont pour but de suivre chaque zone du système avec tous les éléments et paramètres qui leur sont associés. Dans l’écran des limites sont visibles toutes les valeurs extrêmes du système sur chaque élément avec la possibilité d’ajustement par l’opérateur. La liste des messages d’alarme du système est disponible dans l’écran des alarmes.
L’unité de démonstration Multi-AD réalisée a été installée et a été testée sur le système avec la possibilité de la redessiner, pouvant ainsi optimiser son modèle et ses paramètres opérationnels. Enfin, le fait que le réacteur Multi-AD soit entièrement automatisé avec un contrôle avancé fait partie du concept d’industrie 4.0, car notre dispositif utilise un grand nombre de capteurs et met en œuvre des machines de calcul intelligentes, entre autres technologies.