The LIFE Multi-AD 4 AgroSMEs project aims to develop a high-performance multiphase anaerobic reactor for its industrialization, which generates methane-rich biogas, specially designed for wastewater treatment generated in small and medium enterprises in the food and beverage industry.
The successful operation of an anaerobic reactor depends on keeping the environmental factors close to the comfort range of the microorganisms. For example, changes in temperature, pH or organic matter concentration of wastewater can cause biogas production to stop. Thus, keymportant parameters in this process are: temperature, pH, redox potential, organic loading rate, solid and nutrient concentration.
One of the specific objetives of the LIFE Multi-AD project is to develop, optimize and automate the control system to maximize the stability of the anaerobic process and make it robust to changes in wastewater composition or operating conditions. The control system will automatically adjust the controllable output variables (temperature, pH, total suspended solids (TSS), chemical oxygen demand (COD), wastewater flow), using algorithms and logic functions. The main functions of the automation system are: monitoring the level, COD, TSS, temperature and pH in the tanks, displaying the parameters and alerting the operator when the parameters of the normal operating limits are exceeded.
The automation system was developed based on an innovative technological scheme, which includes details on how wastewater from the beverage industry is supplied to the wastewater treatment plant to power the Multi-AD reactor and how the resulting biogas is processed to allow further capitalization.
The LIFE Multi-AD project has successfully completed the development stage of the advanced based control system for automating the control of process parameters. At this stage, based on the results of the previous actions, a 1: 1 demonstration work unit of the Multi-AD reactor on an industrial scale of 100 m3 was built to validate its performance.
SIS part of the project was the automation of the whole process. This journey has started at the design phase, when we analyzed the process and created the best configuration for the automation cabinet of this application. Further, we used TIA Portal V16 to program the logic, using a “Cause-effect” approach, thus interconnecting the whole station and making the operation as safe as possible. Simulation and testing procedures were done by using the extension PLCSim, to ensure that we deliver a logic that works like a charm.
Automation means nothing if you cannot control and monitor it, so we developed two solutions for this application.
The first one is a physical HMI interface, placed on the automation cabinet, created with the help of WinCC Siemens software, it is a graphical representation of the whole station, making it easy for an operator to change set-points, activate and deactivate pumps, monitor values and much more.
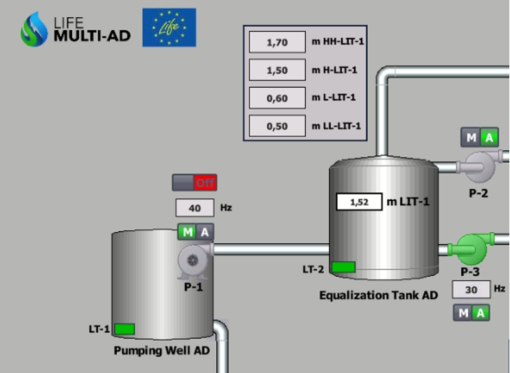
The operator interface consists of ten screens: the main screen, four detail screens, the pump screen, the electrical screen, the timer screen and the alarm screen. The main screen shows the complete scheme of the system and allows navigation through the buttons to the other screens. The detail screens aim to track each area of the system with all the elements and parameters associated with them. In the limits screen are visible all the extreme values of the system on each element with the possibility of adjustment by the operator. The list of system alarm messages is available in the alarm screen.
The realized Multi-AD demo unit was installed and has been tested on the system with the possibility of redesign, thus being able to optimize its model and operational parameters. Finally, the fact that the Multi-AD reactor is fully automated with advanced control is part of the Industry 4.0 concept, as our device uses a large number of sensors and implements intelligent computing machines, among other technologies.
This LIFE Multi-AD project offers an innovative technological solution, ready to be adopted by small and medium enterprises in the food and beverage industry.